Steelmaking is one of the most energy-intensive industries
As an exceptionally strong, malleable and resistant material, parts made from steel form an integral part of almost every building, household appliance or vehicle.
In 2022, the German steel industry produced around 37 million tons of untreated crude steel, which led to around 48.9 million tons of CO2 emissions. This accounts for 29 percent of total industrial emissions in Germany. A large proportion of the carbon dioxide emissions are process-related and result from the coke combustion. Other relevant emissions can be attributed to the use of electrical power generated from fossil fuels. Steelmaking is therefore one of the most energy-intensive industries.
Full decarbonisation requires a technological transition
The industry works continuously to reduce its climate emissions by focusing on efficiency improvements. While further reductions in CO2 are still possible with the technologies utilised to date, their potential savings are not sufficient to achieve the full decarbonisation of crude steel production. For this, a radical technological shift is needed that offers an alternative to the high-emission blast furnace route.
The most promising option for reducing CO2 emissions is to dispense with coke, which is used to reduce iron ore in the blast furnace. In the so-called direct reduction process, hydrogen is used instead as a reducing agent. Natural gas or gas mixtures could also be used as a transitional step that would already achieve significant emissions reductions. The sponge iron produced in this way can then be melted down into steel in an electric arc furnace.
Other options instead focus on capturing the process-related CO2 emissions, either for permanent (underground) storage (carbon capture and storage, CCS) or reuse in some other industrial process (carbon capture and usage, CCU). The industry is currently discussing various combinations of these technologies. However, the processes all have very high additional energy demand and can only capture CO2 to a limited extent.
Using upcoming reinvestments as an opportunity for transformation
Challenges for the steel industry include the decade-long investment cycles. Around half of all blast furnaces in Germany are due for reinvestment by 2030. Accordingly, a solid foundation for the transition to greenhouse gas neutrality must be built up over the coming years. For the implementation, it is imperative that technical and regulatory requirements are considered. For instance, sufficient quantities of renewable energy and green hydrogen must be available locally at the production facility. Since there is no difference in quality between greenhouse gas-neutral steel and conventionally produced steel, market regulators will need to incentivise use of the climate-neutral product. Targeted research is also needed to resolve the existing metallurgical issues resulting from the hydrogen-based direct reduction process. For CCS and CCU approaches, it is necessary to clarify the storage and real-world uses of CO2 in other industries.
Examples from practice
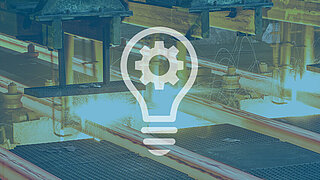
Siderwin
Siderwin is a European project under the Horizon 2020 funding programme. The aim here is to deploy an electrolytic process to reduce iron ore to iron without using a CO2-rich reducing agent. A pilot plant will be built in France by September 2022 to investigate both a prototype electrolytic cell and the use of renewable energy in the process.
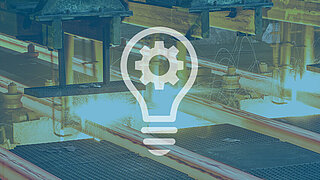
HYBRIT
HYBRIT is an initiative launched in 2016 by SSAB, LKAB and Vattenfall to promote the production of hydrogen-based steel making. In 2020, the first pilot plant for the production of carbon-free sponge iron (direct reduced iron, DRI/hot briquetted iron, HBI) went into operation in Luleå (Sweden). Overall, the project has a potential to reduce CO2 emissions by ten percent in Sweden and seven percent in Finland.