On the path to climate-neutral manufacturing
The non-ferrous metals industry supplies many other industries and areas of day-to-day life. Examples include the use of aluminium, copper and non-ferrous cast parts in healthcare for the production of medical devices, for example. In the food industry, aluminium is used in the outer layers of packaging, helping to extend the shelf life of packaged products. Non-ferrous metals also form an integral part of wind turbine systems and are therefore indispensable for environmentally friendly power generation. Copper is required for the working parts of generators, for example, while an outer layer of zinc provides long-term protection against corrosion for wind turbines.
High degree of electrification for non-ferrous metal production
Depending on production volumes, the non-ferrous metal industry can produce as much as 3.5 million tons CO2 equivalent per year. This corresponds to around 2 percent of all manufacturing greenhouse gas emissions. Of these, around 1.1 million tons CO2 equivalent are process-related. This proportion is relatively low in comparison with other energy-intensive industries, since non-ferrous metal production has already achieved a high level of electrification.
Reducing carbon footprints with high rates of recycling
Many industry businesses started introducing energy efficiency measures many years ago. While carbon emissions in the non-ferrous metals industry amounted to 14.3 million tons CO2 equivalent in 2000, these have since been cut to 3.1 million tons CO2 equivalent (2022, data enquiry Metal Trade Association, Statista ‘Greenhouse gas emissions from manufacturing in Germany by industry in 2021’). This equates to a 75 percent reduction in the initial figure. Improvements are achieved by the ever-growing use of recycled materials. As an example, the energy required to manufacture 1 ton of secondary aluminium is only 5 percent of that required for primary aluminium production. In the production of raw aluminium, the proportion of secondary raw materials used is 58 percent, with a figure of 44 percent for the production of copper. Further improvements to these recycling rates are being pursued for the future.
Mitigating greenhouse gas emissions with electrification
Although the technological potential for mitigating greenhouse gas emissions is industry-specific, the production of primary aluminium within the non-ferrous metals industry takes a leading role here, since more than 80 percent of the process is already handled with electrical energy. Other, non-electrified areas include process heat generation, for example, where fuels are typically used to achieve the controlled heating and cooling that guarantees the metallurgical quality of the raw material. In other processes, the use of biomass or even synthetic fuels is possible, for example.
Research into carbon-free aluminium and copper production
Current research efforts are focusing on transitioning primary aluminium production to carbon-free methods. To produce the molten aluminium, a fuel material must be used that itself generates no greenhouse gas emissions. Tests are being conducted to ascertain whether carbon anodes can be replaced by an inert anode material that would release oxygen instead of CO2. No method has yet been scaled up to industrial production, however.
Research into copper manufacturing is looking into the use of hydrogen, although this method is again not yet usable for large-scale production.
Climate-friendly methods' need in-the-field testing and financing
Many processes in non-ferrous metal production are already optimised. While other measures to improve carbon footprints are technically feasible – such as transitioning to electric furnaces – they are not profitable from an operational business perspective. Incentives for investment need to be created here and operating costs covered by carbon contracts for difference.
The availability of green electricity is also an important factor when it comes to reducing carbon footprints. If the demands of electrified manufacturing processes could be met in full by carbon-free electricity, then it is estimated that carbon emissions could be cut by half. Consistently low electricity prices for industrial customers would also promote the transition from gas-powered to electrical furnaces.
Examples from practise
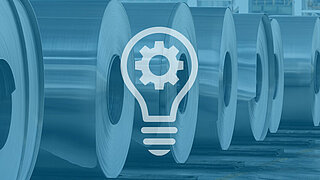
Carbon-free aluminium production
German aluminium maker TRIMET Aluminium SE is working with Arctus Aluminium Ltd. from Iceland to develop an innovative method for aluminium production utilising multiple vertical inert anodes and cathodes in a low-temperature electrolyte (800 °C). The process does not use carbon anodes, so oxygen is released instead of CO2. The inert anode material is being developed in a joint project with Saarland University (USAAR).
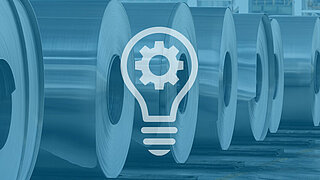
Hydrogen as a reducing agent for copper production
AURUBIS is investigating how hydrogen can be efficiently integrated into copper manufacturing. In an anode furnace, this can replace natural gas as a reducing agent and therefore improve the purity of the copper. Steam is released as a by-product.