In recent years, the industrial sectors have already developed roadmaps and strategies for decarbonising their businesses, many of which rely on entirely new types of production processes. For many industrial sites, this will mean a partial or even complete conversion to new equipment and systems. The focus here will be on technologies that prevent process-related greenhouse gas emissions from occurring in the first place. However, in some sectors (especially in the cement, lime and glass industries), emissions are generated which, according to current knowledge, will remain difficult to avoid even in the future. Carbon capture is therefore being discussed as a possible solution. Which technologies are hidden behind the term and for whom are these technologies relevant?
CCU – CO2 as a feedstock for industrial processes
CCU stands for ‘carbon capture and utilisation’. This means that CO2 is separated out from one (industrial) process or captured directly from the air (direct air capture, DAC) and reused as an input stream for another industrial application. The captured CO2 is turned into a carbon source and therefore a feedstock for chemical or biotechnological processes. It be used to make plastics or synthetic fuels for aviation and shipping, for example, or the CO2 can be sequestered (stored) in building materials. The primary aim of CCU is to sequester CO2 for as long as possible or use it within a closed-loop system.
CCS – CO2 storage in underground deposits
In contrast to CCU, CCS (carbon capture and storage) does not envisage any further use for the captured CO2 but instead stores it permanently underground – typically in a gaseous state. Typical sites for this storage include former natural gas and oil reservoirs. In some countries within Europe, such as Netherlands, Norway and the UK, for example, CCS has either already been deployed or is now being piloted for deployment at the largest possible scale. A different strategy is being pursued in Iceland. In this approach, CO2 is being injected into basalt formations, to which the gas binds (mineralises) in just a few years. In Germany, the 2012 Carbon Dioxide Sequestration Act (KSpG) governs pilot projects for the long-term sequestration of carbon dioxide in underground rock formations and reservoirs. According to the legal situation in Germany, the underground injection of CO2 for long-term storage is ruled out.
Choice of CCU technology critical for greenhouse gas mitigation
There are three main types of CO2 emission produced by industrial processes: direct energy-related, indirect energy-related and process-related CO2 emissions. The first step is therefore to determine whether CO2 emissions can be avoided completely at the outset. Approaches here can include improvements in efficiency, process electrification, the use of hydrogen produced from renewable energy sources or substitution with different materials. Avoiding emissions is always considered to be preferable to the reuse or sequestration of captured CO2.
Use of carbon dioxide in the energy-intensive production of basic materials
With electricity generated from renewables, CO2 can be utilised to produce basic materials (such as methanol) for use in plastics manufacturing or synthetic fuels (e.g. aviation kerosene), for example. When substituted for fossil materials or fuels (such as oil and gas), this results in fewer greenhouse gas emissions being produced. If the CO2 is used in chemical products, this carbon can potentially be kept in a long-term closed loop system – thanks to chemical or mechanical recycling, for example – which ultimately leads to further reductions in CO2 emissions.
Climate change mitigation potential of CCU
CCU technologies can thus contribute to reducing greenhouse gas emissions and therefore to climate protection under certain conditions. All of these depend on large quantities of electrical power and heat, however, and this energy must be produced renewably, otherwise there is a real risk that CO2 emissions end up being higher with CCU than without. In addition, it should also be noted that, for some applications, direct electrification is a more efficient way to utilise the renewable energy. If we take electric vehicles (EVs) as an example, an EV drive system would require only a fifth of the power needed to manufacture a synthetic fuel (via power-to-liquid technologies) to cover the same distance as the synfuel vehicle.
CCU in energy-intensive industries – conditions and sector specifics are key
In assessing the sustainability of CCU technologies, the specific processes and conditions to which CCU will be applied are all-important. Examples of these include the origin of the CO2 itself (fossil, biogenic, atmospheric), the type of use (synthetic fuels, plastics, building materials) and the type of renewable energy source utilised. In certain types of energy-intensive industries (and in the cement, lime and glass industries in particular), however, CCU could be a viable strategy for reducing hard-to-avoid process-related greenhouse gas emissions until other options for avoidance have been developed. For the chemicals industry, CCU technologies are also important over the long term, to make CO2 reusable as a raw material.
Real-world examples
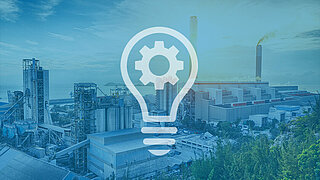
[Translate to English:]
Columbus – microorganisms convert carbon dioxide from lime manufacturing into methane
German biotech start-up Electrochaea has developed a reactor in which single-celled microorganisms (Archaea) convert carbon dioxide and hydrogen into methane. An initial large-scale plant is being planned in Charleroi (Belgium), which will recycle 90,000 t of CO2 captured from lime production. A key feature of this project is that the microbes do not need pure, upgraded CO2 and can ‘renew’ themselves indefinitely. This avoids the energy-intensive process of waste gas scrubbing. By comparison: chemical catalysts need to be replaced every five to ten years.
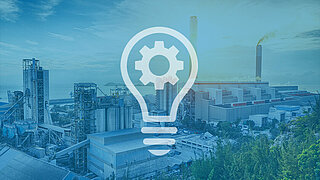
CLEANKER– clean cement clinker production
An international consortium of 13 partners from research, industry and NGOs is working on this project, which is funded by the EU. Together, they are using a cement factory in Vernasca (Italy) to demonstrate a new approach to calcium looping (CaL), which is a promising technology for carbon capture. In Vernasca, the CaL method is integrated as a central part of cement production. In addition, the carrier material deployed in the CaL process is also the same raw meal that it is utilised for clinker production.