WAGEOS2SHS WAGEOS2SHS – Pilotanlage für CO₂-arme Zementklinkerproduktion
Zuwendungsempfangende
Zuwendungsempfänger: Lech-Stahlwerke GmbH, Max Aicher Umwelt GmbH, Holcim (Deutschland) GmbH, Märker Zement GmbH
Projekt: (Verbund) WAGEOS2SHS – Wassergranulation von Elektroofenschlacke zu schwarzem Hüttensand
Maßnahmen
Branche: Zement / Stahl
Projektart: Industrielle Forschung
Laufzeit
01.07.2024 bis 30.06.2027
Verortung
Harburg/Meitingen/Sehnde (Höver) – Bayern/Bayern/Niedersachsen
Fördervolumen
1.563.674,00 €
Copyright: Max Aicher Umwelt GmbH
Bereits im antiken Rom wurden Straßen, Plätze und Häuser aus erstarrter Lava gebaut. Seit gut hundert Jahren sind hingegen lavaähnliche Nebenprodukte aus der Stahlerzeugung wichtige Rohstoffe für die Bau- und Zementindustrie: die Eisenhüttenschlacken. Nun entwickeln die Lech-Stahlwerke und das Recyclingunternehmen Max Aicher Umwelt mit den Zementproduzenten Holcim und Märker einen klimaschonenden Klinkerersatzstoff. Im innovativen Forschungsprojekt bauen die Verbundpartner eine Pilotanlage, die aus der Elektroofenschlacke von recyceltem Schrott eine CO2-arme Rohstoffalternative für die Zementindustrie gewinnt.
Die Herausforderung: Wegfall von Hüttensand für die Zementproduktion
Bei der konventionellen Produktion von Roheisen in Hüttenwerken entsteht bislang bei Temperaturen von rund 1.500 Grad Celsius die schmelzflüssige Hochofenschlacke als Nebenprodukt. Von diesem, der vulkanischen Lava ähnlichen Erzeugnis werden in Deutschland jährlich rund sieben Millionen Tonnen Hüttensand gewonnen. Der feingemahlene Sand wird aufgrund seiner vorteilhaften chemischen und physikalischen Eigenschaften seit Jahrzehnten von der Zementindustrie eingesetzt. Neben Klinker ist der Hüttensand damit ein wichtiger Hauptbestandteil von verschiedenen Zementarten.
Mit der zunehmenden Dekarbonisierung der deutschen Stahlindustrie werden schrittweise klassische Hochöfen stillgelegt und durch mit Grünstrom betriebene Elektrolichtbogenöfen ersetzt. Das bedeutet für die Zementbranche den Wegfall des stark nachgefragten Hüttensandes. Um einen Rückgriff auf natürliche Ressourcen zu vermeiden, wird versucht, die sogenannte Elektroofenschlacke nutzbar zu machen. Diese entsteht bei der elektrifizierten Stahlherstellung während dem Einschmelzen von Stahlschrott.
Die Innovation: Prototyp für CO2-reduzierten Klinkerersatz
Genau dort setzt das geförderte Projekt “Wassergranulation von Elektroofenschlacke zu Schwarzem Hüttensand (WAGEOS2SHS)“ an. Die Lech-Stahlwerke und das Unternehmen Max Aicher Umwelt errichten mit ihren Zementpartnern Märker und Holcim eine Pilotanlage zur Herstellung mehrerer hundert Tonnen eines neuartigen, CO2-armen Klinkerersatzstoffes. Der Prototyp im bayerischen Meitingen soll die Produktion von „Schwarzem Hüttensand“ aus der schmelzflüssigen Elektroofenschlacke großtechnisch demonstrieren.
Mittels Wassergranulation wird die Schlacke rasch abgekühlt, wodurch sie die gewünschte Optik und Qualität erhält. Der gewonnene Schwarze Hüttensand ersetzt schließlich aufgrund seiner ähnlichen physikalischen und chemischen Eigenschaften den konventionellen Hochofenhüttensand in der Zementherstellung – und das bei einem deutlich optimierten CO2-Fußabdruck.
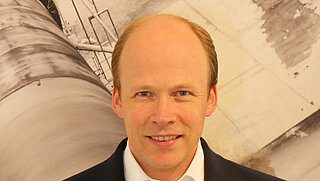
Copyright: Märker Zement GmbH
Wir freuen uns als Familienunternehmen, bei diesem Projekt, welches wegweisend für die Transformation der heimischen Industrie und ein Vorreiter für künftige Technologien ist, mitzuwirken.
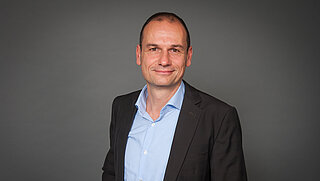
Copyright: Holcim (Deutschland) GmbH
Die Verwendung von wassergranulierter Elektroofenschlacke als Bindemittel ist für uns ein weiterer Schritt auf dem Weg zum klimaneutralen Unternehmen.
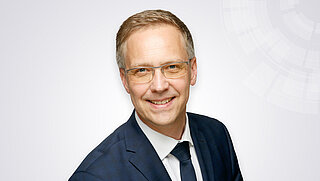
Copyright: Lech-Stahlwerke GmbH
Mit dem WAGEOS-Projekt und der Herstellung von Schwarzem Hüttensand für die Zementindustrie sind wir Vorreiter in der Stahlbranche und leisten einen innovativen Beitrag zur CO₂-Minderung.
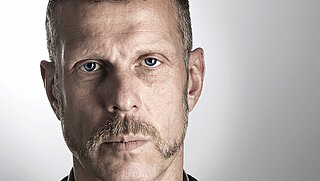
Copyright: Max Aicher Umwelt GmbH
Unser weltweit einzigartiges Projekt zur Herstellung einer CO₂-freundlichen Klinkeralternative entspricht dem, wofür wir hier in Meitingen stehen: zukunftsweisend, nachhaltig und ‚über den Tellerrand‘ schauend.
Der Ausblick: Leuchtturmprojekt für Dekarbonisierung der Branche
Mit der Herstellung eines klimafreundlichen Klinkerersatzstoffes bestreiten die Zement- und Stahlindustrie gemeinschaftlich den innovativen Weg der Dekarbonisierung. Zudem wird die Umwelt geschont, indem Rohstoffe reduziert sowie Brennprozesse vermieden werden. Nicht zuletzt entfallen lange Transportwege: Schwarzer Hüttensand kann künftig dezentral in Deutschland durch die kleineren Elektroostahlwerke produziert werden. Damit werden die Lieferwege zu den umliegenden Zementwerken deutlich kürzer. Zudem werden durch die Verfügbarkeit von Schwarzem Hüttensand auch Importe von klassischem Hochofenhüttensand, etwas aus China oder Brasilien, überflüssig. Das spart zusätzlich CO2 ein.
Der geplante Bau der Pilotanlage ist in der Art und Größe weltweit einmalig. Ziel ist es, die Produktion der „wassergranulierten Elektroofenschlacke“ (WAGEOS) im industriellen Maßstab zu beweisen. Das Projekt ist damit für die gesamte Stahl- und Zementindustrie wegweisend und kann zur Dekarbonisierung dieser energieintensiven Branchen beitragen.
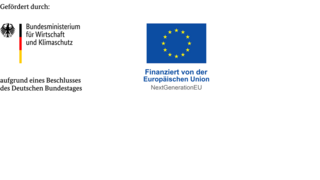